High-Quality Molding & Precision Machining,Which one is better in China?
超级管理员
Views:231
Release time:2024-09-03
High-quality molding and precision machining are pivotal in the manufacturing landscape, especially when it comes to producing components with tight tolerances, complex geometries, and superior finishes. Here’s a comprehensive guide outlining the key aspects, techniques, and benefits associated with high-quality molding and precision machining.
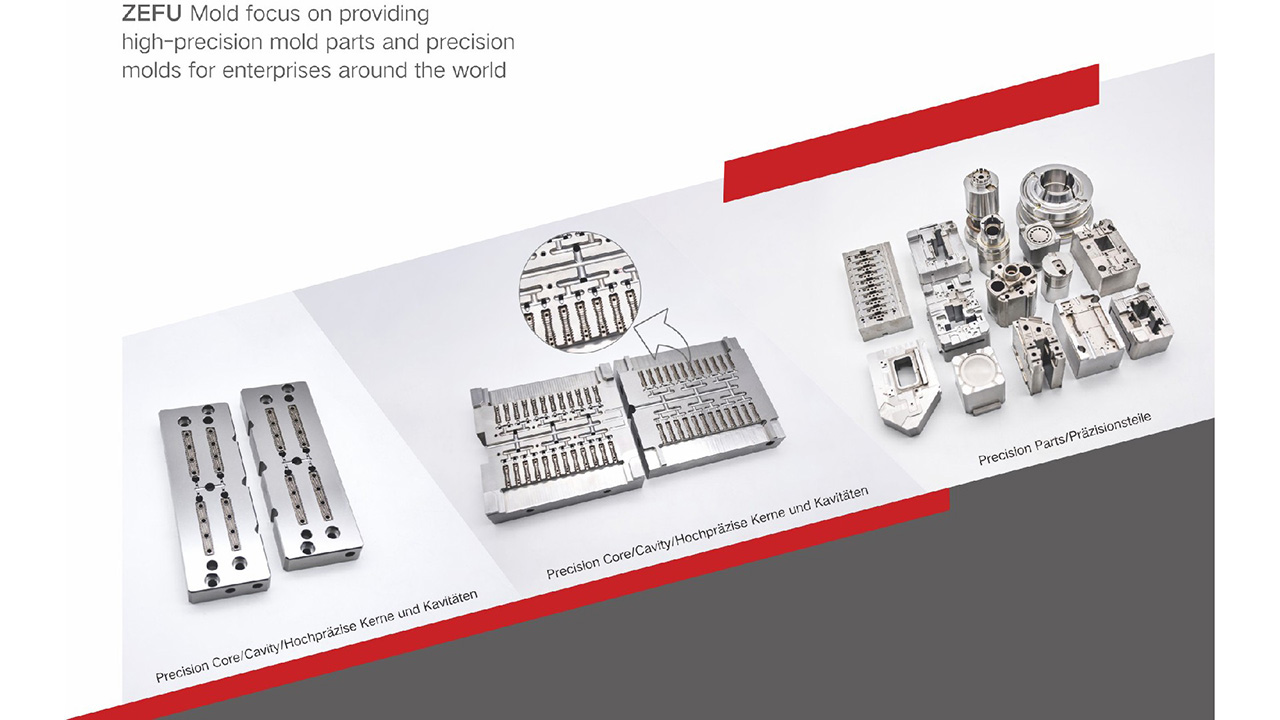
Applications: Widely used for producing complex plastic parts in large volumes.
Materials: Thermoplastics, thermosetting polymers, and elastomers.
Benefits: High precision, excellent surface finish, minimal post-processing.
Applications: Mainly used for hollow parts like bottles and containers.
Materials: Typically thermoplastics such as PET, polypropylene, and polyethylene.
Benefits: Efficient for high-volume production of lightweight parts.
Applications: Used for producing large, relatively simple parts with high strength.
Materials: Thermosetting plastics and composite materials.
Benefits: Cost-effective for large parts, good mechanical properties.
Applications: Used for making large, hollow plastic parts like tanks and bins.
Materials: Primarily polyethylene but can include other thermoplastics.
Benefits: Uniform wall thickness, minimal material wastage.
Precision Engineering: Ensures correct part geometry, consistent quality, and efficient production cycles.
Cooling Systems: Proper cooling channel design to control mold temperature and reduce cycle times.
Compatibility: Choosing materials compatible with the molding process and the final application.
Properties: Considering mechanical, thermal, and chemical properties for optimal performance.
Parameters Optimization: Fine-tuning parameters such as temperature, pressure, and injection speed for consistent quality.
Monitoring Systems: Implementing real-time monitoring for process variables to detect and correct deviations.
Inspection Techniques: Using techniques like visual inspection, dimensional checks, and non-destructive testing (NDT) to ensure part quality.
Standards Compliance: Adhering to industry standards and certifications, such as ISO 9001, to maintain high-quality production.
Applications: Used for creating complex metal and plastic parts with high precision.
Capabilities: Milling, turning, drilling, and grinding.
Benefits: High accuracy, repeatability, flexibility, and efficient production.
Applications: Suitable for hard metals and intricate shapes.
Types: Wire EDM and sinker EDM.
Benefits: High precision, ability to machine hard materials, complex geometries.
Applications: Precision cutting and engraving of metals, plastics, and composites.
Technology: CO2, fiber, and Nd:YAG lasers.
Benefits: High precision, minimal material waste, clean edges.
Applications: Finishing process to achieve high surface quality and dimensional accuracy.
Types: Surface grinding, cylindrical grinding, and centerless grinding.
Benefits: High precision, excellent surface finish.
High-Quality Tools: Using high-quality cutting tools, inserts, and fixtures to achieve precise results.
Tool Life Management: Monitoring tool wear and replacing tools before they affect part quality.
Cutting Parameters: Selecting optimal cutting speeds, feed rates, and depths to balance efficiency and precision.
Coolant Usage: Proper use of coolants to enhance tool life and part quality.
Dimensional Tolerances: Achieving tight tolerances and consistent part dimensions for high-quality assemblies.
Repeatability: Ensuring repeatable results across production runs for reliable performance.
Smooth Surfaces: Producing parts with excellent surface finishes, reducing the need for secondary finishing operations.
Enhanced Properties: Improved surface properties that can affect the mechanical performance and aesthetics of the parts.
Intricate Designs: Enabling the production of complex geometries that would be difficult or impossible with conventional methods.
Innovative Solutions: Allowing for innovative product designs and engineering solutions.
High-Quality Parts: Delivering high-quality parts that meet or exceed industry standards and customer expectations.
Improved Performance: Enhancing the performance and reliability of final products through precise manufacturing.
High-quality molding and precision machining are essential for producing parts with superior accuracy, excellent surface finishes, and complex geometries. By focusing on elements such as mold design, material selection, process control, machine tool accuracy, and tooling, manufacturers can achieve optimal results. These techniques and practices not only ensure the production of high-quality components but also contribute to material efficiency, cost savings, and overall improved performance of the final products.