Spare Injection Mold Components-China Manufacturer, High Precision, Fast Delivery
超级管理员
Views:222
Release time:2024-09-02
Spare injection mold components are critical for maintaining the efficiency and longevity of mold tools in the injection molding process. These components include various parts that can wear out or become damaged over time and need to be replaced to ensure the smooth operation of the molding process. Here’s a detailed overview of common spare injection mold components and their importance:
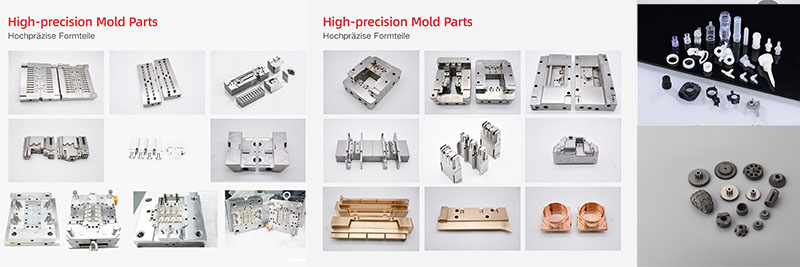
Description: Slides and lifters are used to create undercuts or side actions in the molded part.
Importance: They allow for the creation of complex geometries and are critical for parts with intricate designs. Regular inspection and replacement are necessary to prevent misalignment and part defects.
Description: Ejector pins and sleeves are used to push the molded part out of the mold cavity when the molding cycle is complete.
Importance: These components are subject to significant wear and tear. Timely replacement is crucial to avoid damage to the part or the mold itself.
Description: Core pins are used to form holes or internal features in the molded parts.
Importance: They need to be precisely machined and checked regularly for wear to ensure dimensional accuracy and surface finish.
Description: Guide pins and bushings align the two halves of the mold during closing.
Importance: Proper alignment is essential to avoid flash and ensure part quality. Worn-out guide pins and bushings can lead to misalignment and mold damage.
Description: Runner systems channel the molten plastic into the mold cavities. This can include sprues, runners, and gates.
Importance: Over time, these components can wear, affecting the flow of plastic and part quality. Replacing worn runner system components can maintain consistent flow and reduce cycle times.
Description: Cavity and core inserts are the mold parts that directly form the shape of the molded part.
Importance: These inserts are subject to wear due to repeated cycles of high pressure and temperature. Regular replacement ensures dimensional accuracy and surface quality.
Description: O-rings and seals are used in various locations within the mold to prevent leakage of hydraulic fluids, coolant, or plastic resin.
Importance: Maintaining these components is essential to avoid contamination and damage to the mold or molding machine.
Regular Inspection: Establish a schedule for regular inspection of critical mold components, such as ejector pins, slides, and guide pins.
Documentation: Maintain detailed records of inspections, replacements, and repairs to track component lifespan and performance.
Monitoring Tools: Use monitoring tools and sensors to track mold performance and predict when components will need replacement.
Data Analysis: Analyze production data to identify trends that may indicate upcoming failures, allowing for proactive maintenance.
Wear Tolerance: Replace components when they reach wear tolerance limits specified by the mold design or manufacturing guidelines.
Performance Degradation: Watch for signs of performance degradation, such as increased cycle time, part defects, or mold damage.
Compatibility: Ensure that spare parts are sourced from the original equipment manufacturer to guarantee compatibility and performance.
Quality Assurance: OEM parts typically come with quality assurance and are manufactured to precise specifications.
Cost-Effective Options: Aftermarket suppliers can provide cost-effective alternatives to OEM parts, but it’s essential to ensure they meet required quality standards.
Customization: Some aftermarket suppliers offer customized parts to fit specific mold configurations or requirements.
Lead Time: Consider lead times when sourcing components. Local suppliers may offer faster delivery times, while global suppliers may provide more competitive pricing or specialized parts.
Supplier Reliability: Choose reliable suppliers with a proven track record to avoid delays and quality issues.
Stock Levels: Maintain an optimal inventory of critical spare parts to reduce downtime due to component failure.
Storage Conditions: Store spare components in appropriate conditions to prevent corrosion or damage.
Technical Training: Ensure maintenance personnel are trained in the correct procedures for inspecting, replacing, and maintaining mold components.
Documentation: Provide detailed documentation and manuals for each component to guide proper installation and maintenance practices.
Partnerships: Develop strong relationships with trusted suppliers for reliable access to high-quality spare components.
Collaborative Planning: Work with suppliers to forecast demand and manage lead times effectively.
Maintaining a robust inventory of spare injection mold components is crucial for ensuring the consistent quality and performance of the injection molding process. Regular inspection, timely replacement, and proper management of these components can minimize downtime, reduce maintenance costs, and extend the lifespan of mold tools. By leveraging both preventive and predictive maintenance strategies and sourcing high-quality parts from reliable suppliers, manufacturers can maintain optimal production efficiency and part quality.
Spare Injection Mold Components-China Manufacturer, High Precision, Fast Delivery。